Safe use of chlorine-based disinfectant chemicals guidance
4 August 2023
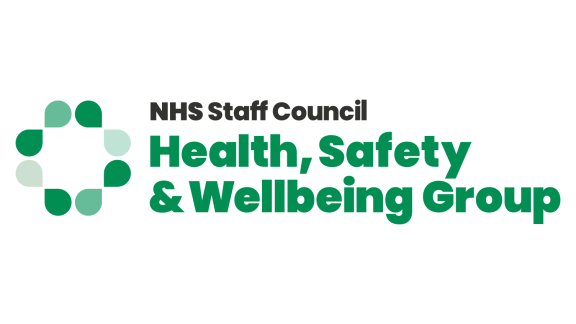
This guidance was developed by the NHS Staff Council's Health, Safety and Wellbeing Group (HSWG), through partnership working between unions, management and specialist advisors.
HSWG recognises that partnership working ensures best outcomes for patients and staff in protecting their health, safety and wellbeing, and wishes to ensure this guidance is implemented with the same partnership approach.
The guidance provides information for health and safety advisors, managers of cleaning staff and trade union health and safety representatives to prevent workers developing respiratory and skin conditions resulting from exposures to commonly-used, chlorine-based cleaning chemicals.
It has been developed for use by the NHS, but the principles can apply to social care or independent sector providers. Organisations that provide contracted cleaning services to the NHS should also follow this guidance.
It focuses on the health risk to workers from exposure to chlorine-based cleaning agents, rather than the issues of infection control and efficacy of cleaning products and methods and issues of patient safety. However, by putting in place measures to protect staff it is likely that patients and the public will also be better protected.
A joined-up approach of cleaning staff working with occupational health, procurement, infection prevention and control, health, and safety, along with estates colleagues, and where they exist contracted cleaning services, will be necessary in order to tackle and reduce any risks to health from exposure.
An appendix added in August 2023 includes a practical workplace checklist to support adherence to the guidance.
-
The COVID-19 pandemic has seen cleaning regimes intensify across UK workplaces, and the health sector is no exception.
While surface cleaning is an essential activity to reduce the spread of biological agents such as Clostridioides difficile (formerly Clostridium difficile), and viruses such as norovirus and SARS-CoV-2, it does come with risks to the workers who are using the chemical cleaning and disinfectant products.
A Health and Safety Executive research report (HSE 2017) found evidence that acute inhalation exposure to chemical cleaning and disinfectant products and persistent low-level exposures from routine cleaning and disinfection tasks may be linked to the development of occupational asthma, exacerbation of pre-existing asthma and potentially other respiratory conditions.
Many health and care workers have contact with chemical cleaning and disinfection products: from directly employed and contract cleaning staff, to catering staff, porters, radiographers and sonographers, paramedics and ambulance crews and nursing and midwifery staff.
However, despite regulations requiring employers to reduce the risk from exposure, a UNISON survey found that only 32 per cent of respondents considered the risk assessment on the use of cleaning chemicals at their place of work to be suitable and sufficient (UNISON 2017).
Workers, who are predominantly women, can also experience a double burden of exposure to cleaning chemicals at home as well as work.
-
A 30-year study by researchers at Harvard University, the French National Institute for Health, and Medical Research (2019) looked at US nurses using disinfectant chemicals and found that there was a 25 per cent to 38 per cent increased risk of developing chronic obstructive pulmonary disease (COPD) with occupational exposure to cleaning products and disinfectants, independent of asthma and smoking.
The researchers looked at a variety of cleaning chemicals including glutaraldehyde, which was still in use at the time of the study, and found a significant increased risk of COPD incidence among nurses exposed to hypochlorite bleach or hydrogen peroxide with or without aldehydes.
While the authors stress that this was an observational study and cannot definitively show that disinfectants cause COPD, they recommend the implementation of exposure-reduction strategies that remain compatible with infection control in health care settings.
Chlorine-based cleaning chemicals can come in a number of formats, from tablet-based preparations that need to be added to water, to wipes, granules and pre-prepared solutions or sprays.
Mixing chlorine-based tablets in hot water can lead to the release of harmful gases and can cause respiratory irritation. Furthermore, chlorine-based disinfectant chemicals should never be mixed with ammonia or acid containing cleaning products as chloramine gases released can lead to serious harm at high concentrations.
Quantities of chloramine gas can also be released when chlorine-based disinfectant chemicals mix with body fluids such as urine especially when large body fluid spillages occur.
Splashes to the eyes can also cause harm from irritation to burns and the extent of damage will depend on the concentration of the product.
A 2017 UNISON survey of members found 60 per cent of respondents who worked in healthcare said they used chlorine based disinfectant products. Members using chlorine-based products reported the following common side effects:
- headaches - 43 per cent
- asthma like symptoms - 52 per cent
- irritation to the eyes - 41 per cent
- nasal discomfort - 34 per cent
- throat irritation - 41 per cent
- skin complaints - 59 per cent.
Those reporting asthma-like symptoms increased from 37.5 per cent to 52 per cent for those who use chlorine-related products.
Along with frequent hand washing/contact with water, chlorine-based disinfectant chemicals can also irritate the skin on the hands potentially leading to work related dermatitis. A 2020 study by the Royal College of Nursing (RCN) found that 93 per cent of nursing staff responding to the survey reported problems with the skin on their hands with dryness, redness and itching being the most common (RCN 2020).
Hand dermatitis can be a debilitating condition and when the skin on the hands breaks down it can present a risk of infection to the worker and to the patients who they may have contact with.
-
Legal
Under health and safety legislation, namely the Control of Substances Hazardous to Health Regulations (COSHH) 2002 and the Control of Substances Hazardous to Health Regulations (Northern Ireland) 2003 (COSHH) (NI), there is a legal requirement for employers to reduce the risk of harm from exposure to hazardous substances at work so far as is reasonably practicable
There are additional requirements to ensure that general ventilation is sufficient under the Workplace (Health, Safety and Welfare) Regulations 1992 and the Workplace Health, Safety and Welfare Regulations (Northern Ireland) 1993.
Where personal protective equipment has been identified as a control measure employers must ensure the supply, provision and use of equipment is complaint with the Personal Protective Equipment at Work (Amendment) Regulations 2022 and the Personal Protective Equipment at Work Regulations (Northern Ireland) 1993.
Where cleaning work is contracted out, the provisions within the Management of Health and Safety at Work Regulations 1999 and the Management of Health and Safety at Work (Northern Ireland) Regulations 2000 apply in terms of the host employer (the NHS organisation) and the contractor communicating and co-operating effectively on any health and safety risks to staff or others from their respective work activity.
A 2008/9 HSE inspection campaign looking at the management of work-related dermatitis in the NHS found serious deficiencies in the way that organisations were assessing, reducing, and monitoring the condition.
Further information on compliance with the law and what this means in practice is detailed below.
Cost
There have been a number of personal injury claims taken by unions on behalf of healthcare workers who have developed serious lung conditions and/or sustained long term damage from working with chlorine-based disinfectant chemicals. Settlements and payments are often large amounts due to the debilitating impact of lung conditions on the individual and the employer’s failure to reduce the risks so far as is reasonably practicable.
Detailed below are two personal injury cases relating to exposure to chlorine-based chemicals.
Moral
No one should be harmed by the work that they do. Lung and skin conditions can be severely debilitating for workers and can in some cases lead to permanent disabilities and difficulties in seeking and retaining employment. As a provider of healthcare, the NHS has a moral duty to protect the health and safety of all its workers from harm, including contractors or agency staff.
-
Control of Substances Hazardous to Health Regulations 2002 and the Control of Substances Hazardous to Health Regulations (Northern Ireland) 2003
The Control of Substances Hazardous to Health (COSHH) Regulations are the key regulations to follow when reducing the risk of harm from exposure to cleaning and disinfectant chemicals.
The regulations require all employers to suitably and sufficiently assess the risk of exposure to hazardous substances in the workplace and where exposure cannot be prevented, to identify adequate ways of reducing the risk, so far as practical. This assessment should be carried out before any work takes place which is liable to expose any workers to a substance hazardous to health.
COSHH assessments should be carried out by a competent person, who understands hazard and risk; knows how the work can expose people to substances hazardous to health; has the ability (and authority) to collect all the necessary information and has the knowledge, skills, and experience to make the right decisions about how to adequately control exposure.
The following guidance on COSHH assessments on the use of cleaning and disinfectant chemicals has been adapted from the HSE’s step by step guide to COSHH assessments.
1. Gather information about the substances, the work, the working environment and the working practices
The following questions should be considered with answers mapped against local guidance, manufacturers recommendations and local policies:
- What product is being used?
- What do the safety data sheets say about the harmful properties of the product?
- What is the potential of the substance causing harm?
- How might staff be exposed?
- Routes of entry to cause harm to the user?
- Who is exposed or potentially exposed (include contractors, agency staff)?
- Are there any workers who could be more at risk from exposure?
- How often is the product being used or advised to be used?
- What quantities is (or should) the product used?
- What form/concentration does the product come in?
- Is the product being used close to the workers breathing zone (the area immediately surrounding a worker’s nose and mouth where the majority of air is drawn into their lungs)?
- Where is the product being prepared and used?
- What level of ventilation is present where products are prepared and used?
- How is the product being prepared and used?
- How is the product being applied to the surface?
To help inform the assessment, managers or the competent person carrying out the risk assessment should speak to staff and their representatives about any concerns they have regarding exposure or potential exposure to the products. When reviewing COSHH risk assessments, managers and safety representatives can also observe working practices to see how and when workers are potentially exposed and assess if the identified control measures are sufficient.
2. Deciding on the necessary measures to comply with regulations 7 to 13 of COSHH
Consideration where it is reasonably practicable to prevent exposure to those hazardous substances by elimination or substitution of the product to one which is less harmful to health?
Do areas need to be cleaned with chemicals, for example, can they be damp dusted? Are there areas where chlorine-based disinfectant chemicals don’t have to be used? Assess the infection risk of each area and select an appropriate product or technique in consultation with your IPC expert. (NB: Seek IPC advice when carrying out assessment and refer to national cleaning standards)
If prevention is not reasonably practicable, what measures can you use to reduce the risk?
- Substitution: Are there safer alternative cleaning chemicals available? (NB: Seek IPC advice when carrying out assessment and refer to national cleaning standards)
- Engineering controls: Are there safer ways of using the chemical? For example use of an aerosol (trigger spray) delivery system leads to a higher risk of exposure – perhaps move to a foam-based system, wipes, or mopping/wiping with a solution.
- Engineering Controls: Can you control exposure at source? For example through closed mixing systems, or local exhaust ventilation when preparing and/or mixing chemicals? Can you also increase general ventilation in areas where there is a higher risk of exposure, such as in the cleaner’s storeroom where chemicals are prepared?
Regulation 4, by virtue of Regulation 6 of the Workplace (Health, Safety and Welfare) Regulations 1992 and the Workplace (Health, Safety and Welfare Regulations (Northern Ireland) 1993) relates to ventilation and places a duty on employers to ensure that every enclosed workplace is ventilated by a sufficient quantity of fresh or purified air.
Good ventilation is important in environments where chlorine-based cleaning chemicals are being prepared and used. Small cleaning rooms with no natural or mechanical ventilation can present a risk when preparing or using chlorine-based cleaning chemicals.
General ventilation:
- All workplaces need an adequate supply of fresh air. In the guidance to Regulation 6 of the Workplace (Health, Safety and Welfare) Regulations 1992, the HSE recommends that the fresh air supply rate should not normally fall below five to eight litres per second per occupant.
- This can be natural ventilation, from doors, windows etc or controlled, where air is supplied and/or removed by a powered fan.
- Dependent on the COSHH risk assessment, natural ventilation in the area where cleaning chemicals are prepared, for example from open windows may be sufficient to control dusts and vapours emitted from cleaning materials etc. Sometimes planned, powered general ventilation is an integral part of a set of control measures.
- Air vents should not be blocked and should be regularly checked/maintained to ensure a flow of air.
- Mechanical ventilation systems should be well maintained.
Local exhaust ventilation:
- Local exhaust ventilation (LEV), often referred to as extraction, is an engineering control solution which removes potential exposures to dust, mist, fume, vapour, or gas at source.
- Effective LEV will prevent the release of harmful substances into the working environment, including the breathing zone of the individual.
- LEV systems can be part of a fixed installation, a portable unit, or form an integral part of a propriety mixing system.
Under Regulation 9 of COSHH, LEV must be thoroughly examined and tested at least every 14 months by a person competent to do so and be maintained in good working order. It is important that when using LEV it is fit for purpose and users have been provided with adequate information, instruction, and training regarding its use.
Other factors that need to be considered (administrative controls):
- Provide sufficient information, instruction and training for employees and others who might be affected. Employers must provide training to workers at a level and in a language and vocabulary that they can understand. Colour-coded systems, visual graphics such as posters and videos can support the safe use of cleaning chemicals.
- Make sure identified control measures are properly used, by talking to staff, and providing good supervision to ensure staff understand how to work safely.
- Where workers are exposed or potentially irritant substances, appropriate health surveillance should be provided. For example, regular skin checks.
- Having an emergency plan in place, ensuring that staff are aware of the plan and have been trained in its operation if something goes wrong e.g., a large spillage of chlorine-based product.
- Ensure staff have adequate time and resources to prepare and use cleaning chemicals safely.
- Make staff aware of how to report incidents or near misses and encourage staff to report any incidents or ill health related to exposure to cleaning chemicals, so that these can be followed up in a supportive rather than a blame culture.
- Monitor the effectiveness of your control measures, for example through cases of dermatitis or respiratory problems, sickness absence amongst groups of workers using cleaning chemicals, incident reports and audits.
Health surveillance
Frequency of health surveillance should be based on risk assessment. However, any formal health surveillance programme should be supplemented by regular manager or supervisor checks. Managers or supervisors must be suitably trained to spot early warning signs, and that employees themselves should have sufficient information and/or training to be able to identify possible issues themselves COSHH health surveillance - COSHH (hse.gov.uk).
Below is some suggested content for health and safety training for staff using cleaning products:
- health and physical hazards of the cleaning chemicals
- proper handling, use and storage, including dilution procedures
- spillage and emergency procedures
- what personal protective equipment to wear and how and when to wear it and dispose of it safely
- explanation of any hazard warning symbols
- how to report concerns, near misses and incidents.
Personal Protective Equipment (PPE)
PPE is a last resort, but when other control measures are not possible and/or the residual risk remains, PPE should be considered. The following are examples of PPE that can be used:
- Eye protection where there remains a risk of splashes to the eyes.
- Gloves where there is skin contact with the product.
- Respiratory protective equipment (RPE): where cleaning and disinfectant chemicals are being prepared or used in poorly ventilated areas and cannot be prepared elsewhere and a residual risk remains (Health and Safety Executive 2022). RPE needs to be selected based on the risk that is being controlled. For example, a face fit tested respirator with a vapour filter to prevent exposure to harmful gases. For more information on selection and testing of RPE see Respiratory protective equipment at work: a practical guide.
3. Record and review the COSHH assessment
Employers with five or more employees must record the COSHH risk assessment. Assessments should be reviewed on a regular basis including when there are any changes to the product being used, including how it is used, and the environment it is being prepared and used in. Assessments should also be reviewed in light of new guidance, where the results of health surveillance indicate concerns or where there are incidents/cases of occupational ill health in workers.
Hierarchy of controls
-
Workplace (Health, Safety and Welfare) Regulations 1992 and the Workplace (Health, Safety and Welfare Regulations (Northern Ireland) 1993
- Regulation 21 to 25 of the Workplace Health, Safety and Welfare Regulations outlines basic welfare requirements for workers.
- Staff who are involved in cleaning tasks, especially cleaning staff, will need access to facilities such as lockers and showers, drinking water and somewhere to eat and rest without the risk of cross contamination.
The NHS Staff Council’s Health, Safety and Wellbeing Group (HSWG) has developed guidance to support NHS organisations to improve their provision of staff welfare facilities.
Personal Protective Equipment at Work (Amendment) Regulations 2022 and the Personal Protective Equipment at Work Regulations (Northern Ireland) 1993
Eye, skin, and respiratory protection may be necessary for those exposed to cleaning chemicals; the use of personal protective equipment should be identified following risk assessment. Where personal protective equipment has been identified to reduce the risk of exposure it must provide adequate protection and be suitable and sufficient in line with the Personal Protective Equipment at Work Regulations.
Management of Health and Safety at Work Regulations 1999 and the Management of Health and Safety at Work (Northern Ireland) Regulations 2000
Regulation 12 of the Management of Health and Safety at Work Regulations 1999
requires host employers to communicate with contractors, on health and safety risks and provide information on how risks are managed.The HSE guidance on contractors
- Do a suitable and sufficient risk assessment – you and the contractor should be aware of its findings. You should already have a risk assessment for the work activities of your own business. The contractor must assess the risks for the contracted work and then both of you must get together to consider any risks from each other's work that could affect the health and safety of the workforce or anyone else who may be affected by the work.
- Provide suitable and sufficient information, instruction, and training to your employees. You should also provide any relevant information to contractors on the risks from your activities and the controls you have in place. It may also be beneficial to consider, with the contractor, what instruction and training contractors will need.
- Set up liaison arrangements for co-operation and co-ordination with all those responsible to ensure the health and safety of everyone in the workplace.
- Decide what you need to do to manage and supervise the work of contractors and agree the nature of the controls before work starts.
Reporting of Injuries Diseases and Dangerous Occurrences Regulations 2013 and the Reporting of Injuries, Diseases and Dangerous Occurrences Regulations (Northern Ireland) 1997 (RIDDOR)
Certain cases of occupational diseases need to be reported under the RIDDOR regulations including cases of work-related dermatitis and occupational asthma. Incidents of asphyxia due to exposure to chemicals are also reportable under RIDDOR. Accidents must be reported where they result in an employee or self-employed person being away from work, or unable to perform their normal work duties, for more than seven consecutive days as the result of their injury.
Safety Representatives and Safety Committee Regulations 1977 and The Safety Representatives and Safety Committees Regulations (Northern Ireland) 1979
Under these regulations there is a duty on employers to consult with trade union health and safety representatives on any matters affecting the health and safety of the workforce.
Trade union health and safety representatives also have a right to the following:
- make representations to management on health and safety issues on behalf of the employees they represent
- investigate accidents, near misses, and other potential hazards and dangerous occurrences in the workplace
- investigate complaints made by an employee they represent about their health, safety, or welfare in the workplace
- inspect the workplace at regular intervals, following concerns and accidents/dangerous occurrences
- set up and attend a health and safety committee when two appointed representatives, request in writing
- attend health and safety committee meetings as a representative of employees
- represent employees when Health and Safety Inspectors from HSE or local authorities consult them.
In relation to cleaning chemicals, trade union safety representatives should be consulted on COSHH risk assessments, policies and the measures employers are putting in place to reduce the risk. They should also be consulted on the planning and delivery of any health and safety information and training.
They can inspect the work environment of their members to ensure that safety measures are in place and speak to members about their concerns.
Union representatives can also ask for anonymised data and information relating to incidents/work related ill health related to cleaning chemicals and any other relevant information held by the employer.
Furthermore, they can make representations about health and safety issues relating to cleaning chemicals or any other health and safety issues to the employer and attend health and safety committee to discuss any concerns.
For further information on health and safety legislation, please see the HSWG workplace health and safety standards.
Case study
An outbreak of an infectious agent necessitated decontamination of large quantities of portable reusable (communal) equipment. The equipment was being moved to a small room with no ventilation to be decontaminated. The decontamination process took approximately 15 minutes to compete. Several staff complained of itchy running eyes and noses from the decontamination activity.
The health and safety manager and union safety representative visited the area to check on how and where the cleaning products were being used. While staff were following protocols for the preparation of the cleaning solution, the room being used was poorly ventilated.
The health and safety manager and union rep identified another area for staff to use which met with infection prevention and control requirements and had better ventilation. Complaints of irritation subsided and staff were able to continue with the ongoing decontamination of equipment.
The checklist in the appendix can also be used to support legal compliance with COSHH and other regulations.
-
Dumas, O. Varraso, R. Boggs, K, M. et al (2010) Association of Occupational Exposure to Disinfectants with Incidence of Chronic Obstructive Pulmonary Disease Among US Female Nurses. Occupational Health; 18 October 2019.
Health and Safety Executive (2017) A literature review of evidence of cleaning products and occupational risk for asthma.
Health and Safety Executive (2022) Research summary - Research on hospital cleaners' use of Respiratory Protective Equipment (RPE) - research conducted by Kantar Public UK.
Royal College of Nursing (2020) Survey exploring skin health issues among nursing staff in the UK: results of a national survey.
UNISON (2017) Keeping Clean and Keeping Safe: a UNISON report on the use of chemicals to combat superbugs.
-
- Control of Substances Hazardous to Health (COSHH)
- Occupational asthma - Asthma + Lung UK
- COSHH and cleaners - key messages
- HSE - Skin at work: what are work-related skin diseases?
- A rapid review of disinfectant chemical exposures and health effects during COVID-19 pandemic
- NHS cleaning standards
- COSHH risk assessment - healthy working lives
-
Download a comprehensive checklist to help support your staff to follow the guidance and stay safe in workplace settings:
Become a member of HSWG
If you work within health, safety and wellbeing in an NHS organisation and are interested in becoming a member of HSWG, please email us to express your interest.
Find further HSWG resources to support you in your organisation.