Sewing the way to sustainability
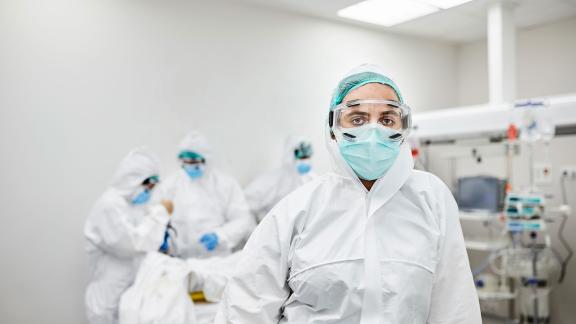
Northumbria Healthcare NHS Foundation Trust engaged with staff and innovated to help tackle the UK-wide shortage of personal protective equipment (PPE) during the initial peak of the COVID-19 pandemic, by producing its own. This provided locally made, high-quality PPE to the NHS, while also creating a much more resilient supply chain.
Key benefits and outcomes
- Sustainability: reducing reliance on global resource chains and creating a much stronger local supply chain.
- Supporting the local economy: as well as providing equipment for staff, the project created jobs for local people and helped support the local economy during a very difficult period.
- Working with the local community: the trust engaged former professional clothes machinists and volunteers living in the local community to help bring the project to life at a point of acute shortage in the NHS.
What the organisation faced
The COVID-19 pandemic caused disruption and uncertainty worldwide, vital supply chains were broken, and national lockdowns became a way of life for millions of people in the UK and billions globally.
At the beginning of the pandemic, a sudden demand arose for PPE at a local level for health and social care providers. This demand quickly outstripped national supply leading to shortages and a need for innovative thinking.
Northumbria Healthcare NHS Foundation Trust faced the dual problem of both needing to keep staff safe while also seeing shortages of the correct PPE. At the height of the crisis, the trust only had 30 gowns in its central stores at a point where it was using around 400 isolation gowns per day. It also experienced considerable concerns regarding the quality of the gowns received, which were being made almost entirely overseas.
What the organisation did
Recognising that the trust’s PPE supplies had reached a critical level, Sarah Rose, a local veteran of the textile manufacturing business with 30 years of experience in the field, offered to help. Sarah was later employed by Northumbria Healthcare NHS Foundation Trust.
Ex-machinists, as well as locals who had been furloughed or lost their jobs, volunteered to help. NHS England contributed £13.2m to help start the initiative and a temporary home was found for the factory in a warehouse.
The team of machinists, some employed by the trust and some volunteering, initially worked to produce basic gowns, theatre hoods and scrubs, but later branched out to add surgical gowns, pillows, patient safety mitts, and other items to the list.
Clinicians were heavily involved in the development of the gowns, and Sarah and the team were dedicated to designing and producing the best possible PPE. Many hours were spent analysing and designing, with the results being incredibly innovative. The medical sector had never seen textile technology like it: seams were redesigned, and new fabrics and weaves were created which continue to have a lasting impact.
Results and benefits
By the summer of 2021, the workforce was no longer just a voluntary one, and the manufacture of the PPE material and garments had become established as a permanent business. The team moved out of the make-shift factory and into a 25-acre site, secured by the Northumbria Healthcare NHS Trust, making the work part of the trust’s establishment.
Not only had the project team changed PPE design and production forever, but it also offered out-of-work machinists an opportunity to get back into the career they loved, as well as providing jobs and a purpose to a community that was struggling with the overwhelming impact of the pandemic and the loss of so many lives. With growing demand, the factory expanded its workforce to 60, and created 10 apprenticeships for local people in an area of high unemployment.
Thanks to Northumbria Healthcare NHS Trust young people across the region now have the opportunity to apply for positions in sewing, cutting, warehouse, business administration and machine mechanics; something that would not have been possible before.
Overcoming obstacles
The gowns and scrubs had to pass many stringent tests to make sure they were compliant with the Health and Safety Executive’s (HSE) and Medicines and Healthcare products Regulatory Agency’s (MHRA) infection protection standards, before being deemed safe for use.
For a period of three months, all the garments that were produced had to be quarantined until the CE mark could be given. Once this was passed, the garments were all signed off by the HSE and were ready to be used.
Going forwards
The project has been a huge success – so much so that the trust had to purchase a bigger site (40,000 sq/m) to run the operation from. Seeing through its two millionth gown milestone at the end of 2020, the innovative venture is paving the way for the future of PPE provision for the health sector.
All of this work has helped to bolster the trust’s Community Promise, the site has created change for the better in not just healthcare, but the wider education, employment, and economic aspects of people’s lives.
As the intensity of the pandemic has changed, the factory no longer just deals with PPE equipment. The team now also manufactures items such as picnic blankets and bags. These are used by the hospital in gift packs for prizes, and welcome packs for new staff.
The outstanding health trust was awarded for its Manufacturing and Innovation Hub, based in Seaton Delaval, which produces PPE and other medical supplies for health care services.
Take away tips
- Engage with the local community to find a pool of talented professionals from different backgrounds and industries who can help the NHS tackle its current challenges in an innovative manner.
- Encourage an open-minded and resourceful approach to problem-solving, and create a space where people feel safe to share their ideas.
- Strive to make a difference not only in the health and care sector, but also in the wider community.
Further information
You can watch a brief video about the factory via YouTube.
For more information, please contact us via email at workforcesupply@nhsemployers.org